Next Level S&OP
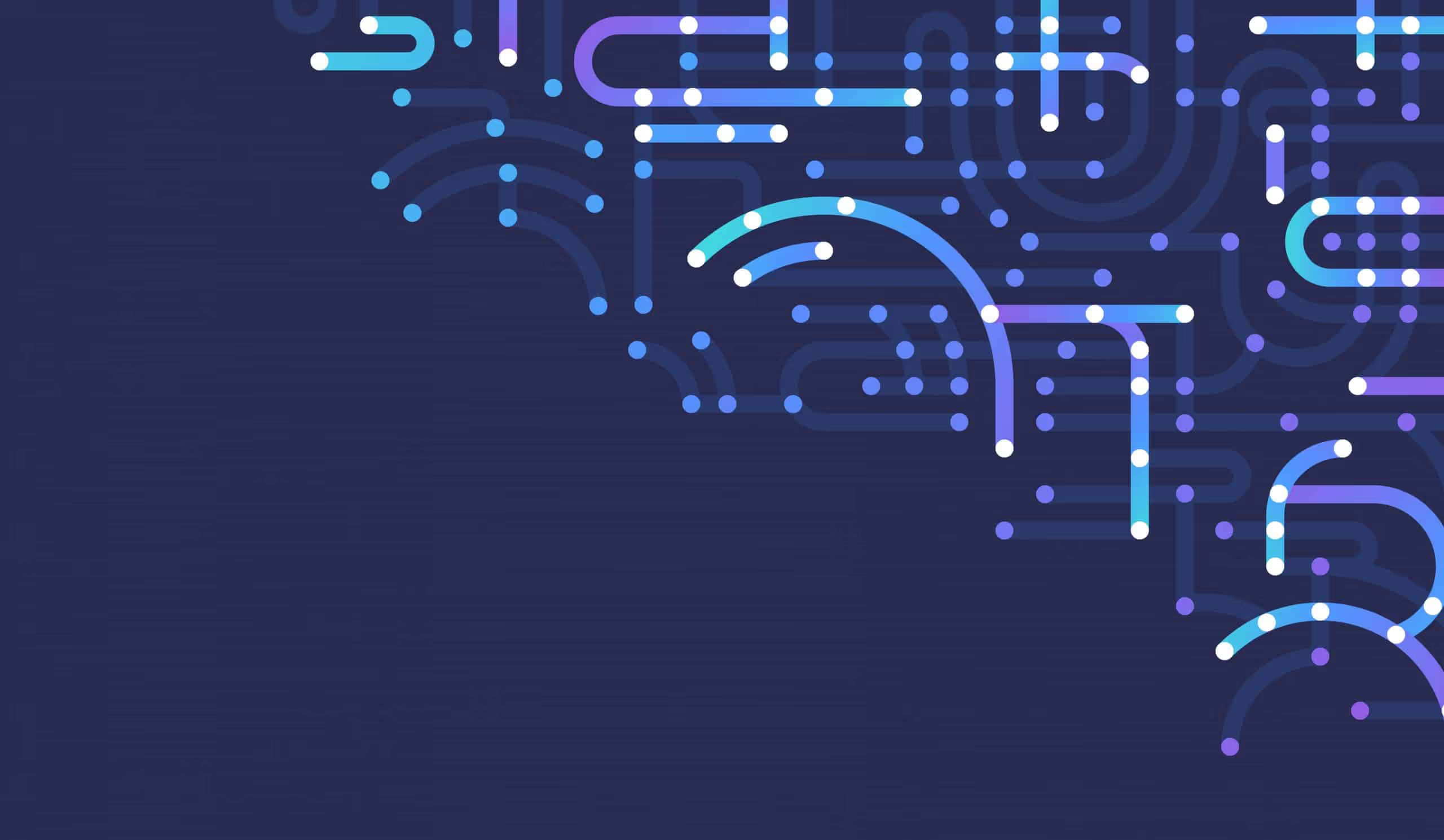
Better planning accuracy thanks to integrated process analysis
How process mining can dramatically increase the quality and speed of your sales & operations planning (S&OP).
To ensure smooth operations in a company's supply chain, numerous departments must be in close coordination. With silo thinking and scattered Excel lists, however, it is almost impossible to network the individual value creation processes in such a way that everyone involved has the information they need for their tasks. With serious consequences: There is a risk of delivery problems, capacity bottlenecks and incorrect or excessive stock levels.
Excel solutions reach their limits
The planning process with the greatest influence on the organization and thus in manufacturing companies the "mother of all planning" is the coordination between customer demand and production planning.
This includes:
- Sales Forecast (demand development, campaigns, novelties, outgrowers, new clients)
- Production-side mapping of requirements (routings, bills of materials, capacities, material logistics)
- Coordinated supply plan including capacity adjustments, optimal lot sizes, and inventory metrics
- Analysis of financial impact of reconciled plans on P&L and balance sheet
Frequently, these individual partial plans are not only carried out by different people, but also in different systems. Bringing demand and supply into line with each other and creating a networked plan across the entire organization is accordingly associated with an enormous coordination effort and can therefore only really be meaningfully solved with the help of an integrated planning tool. Actual data analyses, forecasting algorithms, work flow control and add-ons such as HR planning modules or the automatic creation of P&L, balance sheet and cash flow based on the plan data round off the package.
Basic parameters for a functioning S&OP planning are assumptions e.g. about capacities, processing times and availabilities. These assumptions are either completely theoretical or are determined sporadically by manual measurements or capacity evaluations. Whether a team or a machine is capable of producing 80 finished parts per hour or perhaps rather 100 makes a big difference, and not only for actual order processing. If this figure is used as an input parameter for tool-based planning, the planning result may deviate greatly from reality. Thus, there is a risk that the sales forecast has to be reduced or, conversely, that production facilities are not well utilized because the production capacity is assumed to be too low. Process mining based on process or log data already available in the company closes this gap and replaces assumptions with reliable key figures.
Conclusion
The integration of process mining into planning makes it possible to verify and correct these mostly theoretical assumptions through ongoing analysis of the underlying operational processes. Instead of sporadic measurements, performance within a process is continuously monitored. Process disturbances, bottlenecks and trends in throughput times become visible and can be directly addressed through data integration of process mining and planning data. But that's not all: If the planning result does not meet expectations, process mining provides the reasons for a surprising shortfall in a specific product, for example. In this way, disruptions or deviations from the target process can be identified in detail almost in real time during the current planning round and measures can be derived to eliminate them. Planning has never been closer to reality.