Data dump or gold mine?
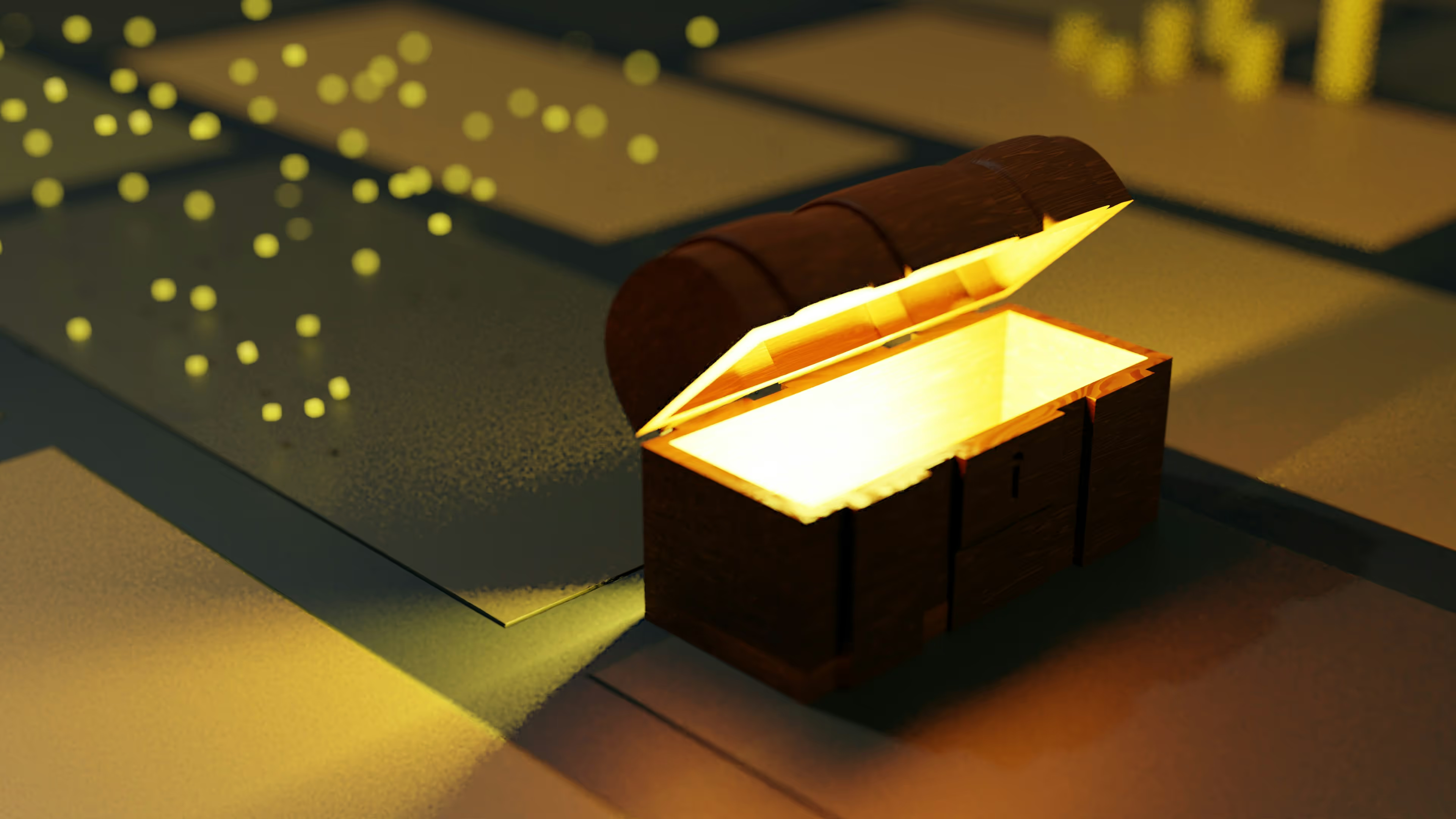
Cash flow optimization with process mining
Process Mining: Waste of Resources or Treasure of Data?
In many companies, extremely valuable data simply lies around unused: transaction or event logs, for example from ERP, CRM, production control or the ticket system. This data is usually available anyway, but little attention is paid to it and it often only eats up system resources. Yet they form the basis for generating a comprehensive digital view of business processes with comparatively little effort and immediately deriving measures for optimization.
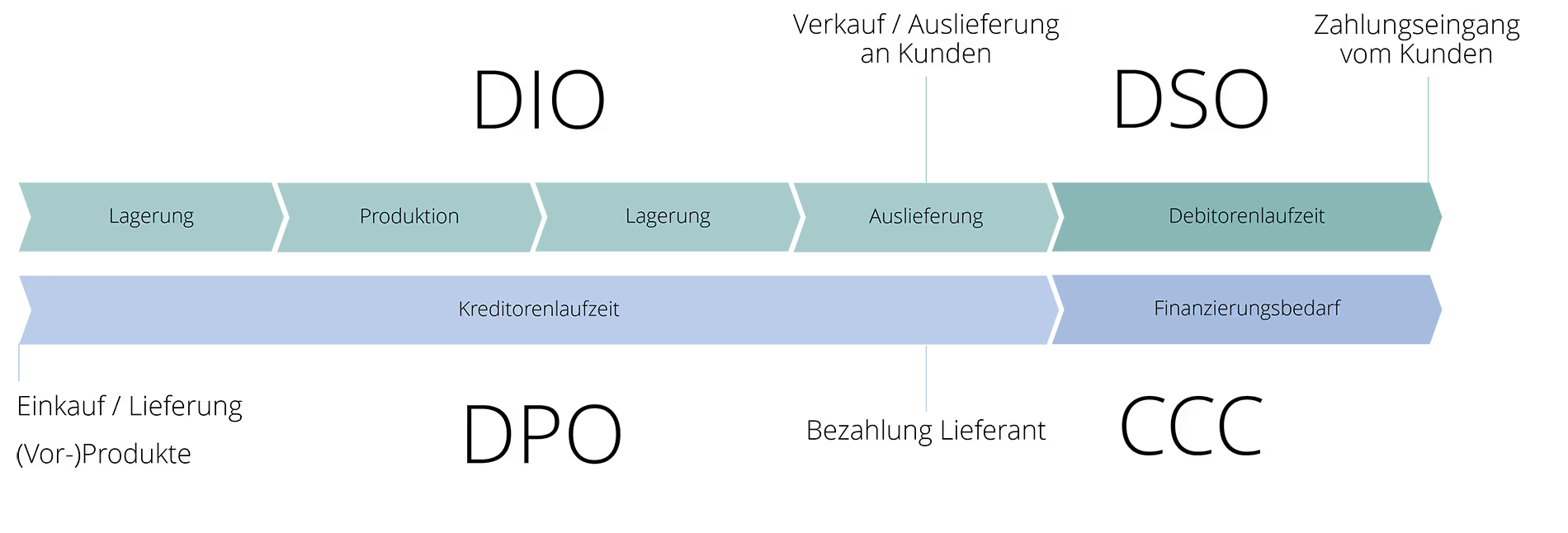
Liquidity optimization yesterday and today
Classically, attempts are made to influence the available cash reserves by adjusting payment terms and short-term liquidity planning. In fact, some important reasons for, for example, a late payment by the customer or the loss of discounts at the supplier already lie in preceding process steps. So for a real optimization of payment flows, we need to start much earlier and look at the individual transactions, which is almost impossible without appropriate tools.
Process mining applications analyze the process on the basis of all individual transactions and identify these weaknesses. By linking them to master data and amounts from the associated documents, they show the (monetary) impact on the company as a whole and offer approaches to identify where improvement measures are worthwhile. In this way, they provide insights that can lead to significant improvements in all the above-mentioned process strands, also with regard to the cash situation. Here are some examples from the three areas mentioned:
- Purchasing: Our primary objective in the purchasing process - in terms of the cash conversion cycle - is to optimize the accounts payable period. Too late a payment costs us money in the form of lost discounts, and too early a payment in turn worsens our cash situation. In addition, we have to ensure that we comply with certain specifications and that we only make correct payments.
- Sales: In sales or order processing, it is important to get to invoicing as quickly as possible. In addition to price and quantity discrepancies, even minor errors, e.g. in customer master data, lead to major delays, for example because bookings have to be cancelled and re-executed or customers need clarification or even have a reason to complain.
- Warehouse/production: It is clear that the shortest possible storage period is good for the liquidity situation. However, it is also important to deliver goods to our customers as quickly as possible in order to be able to issue an invoice as early as possible. Depending on the industry, there are an enormous number of fundamentally different sub-processes in warehouse logistics and production.
All in all, there is a wealth of processes and sub-processes that have a significant influence on our liquidity. We cannot even begin to gain an overview of the majority of them, let alone evaluate them, simply by looking at the operational system, observing them or holding workshops with those involved in the processes. However, the basis for being able to do this, to uncover weaknesses and derive measures, is available: The existing log files from the IT systems in use, which tell us exactly what happened where and when. You can think of it as a digital footprint of all transactions. With the help of process mining, we are able to visualize them and discover the huge potentials that lie in our processes. A well-known provider of process mining software is currently advertising that it will donate 100,000 USD if it does not find at least 10 million USD in potential savings in participating companies. Anyone who has studied process mining a little will hardly doubt that donations will probably not be necessary.
The implementation of such a process mining solution is relatively quick and easy. The required data is already available, the process experts are already in the company, and the tool providers have ready-made templates in their portfolio that can be easily adapted to the individual circumstances for standard processes. Through integration into existing BI landscapes, a new infrastructure is not even required, so that initial results can be achieved within 1-2 weeks.